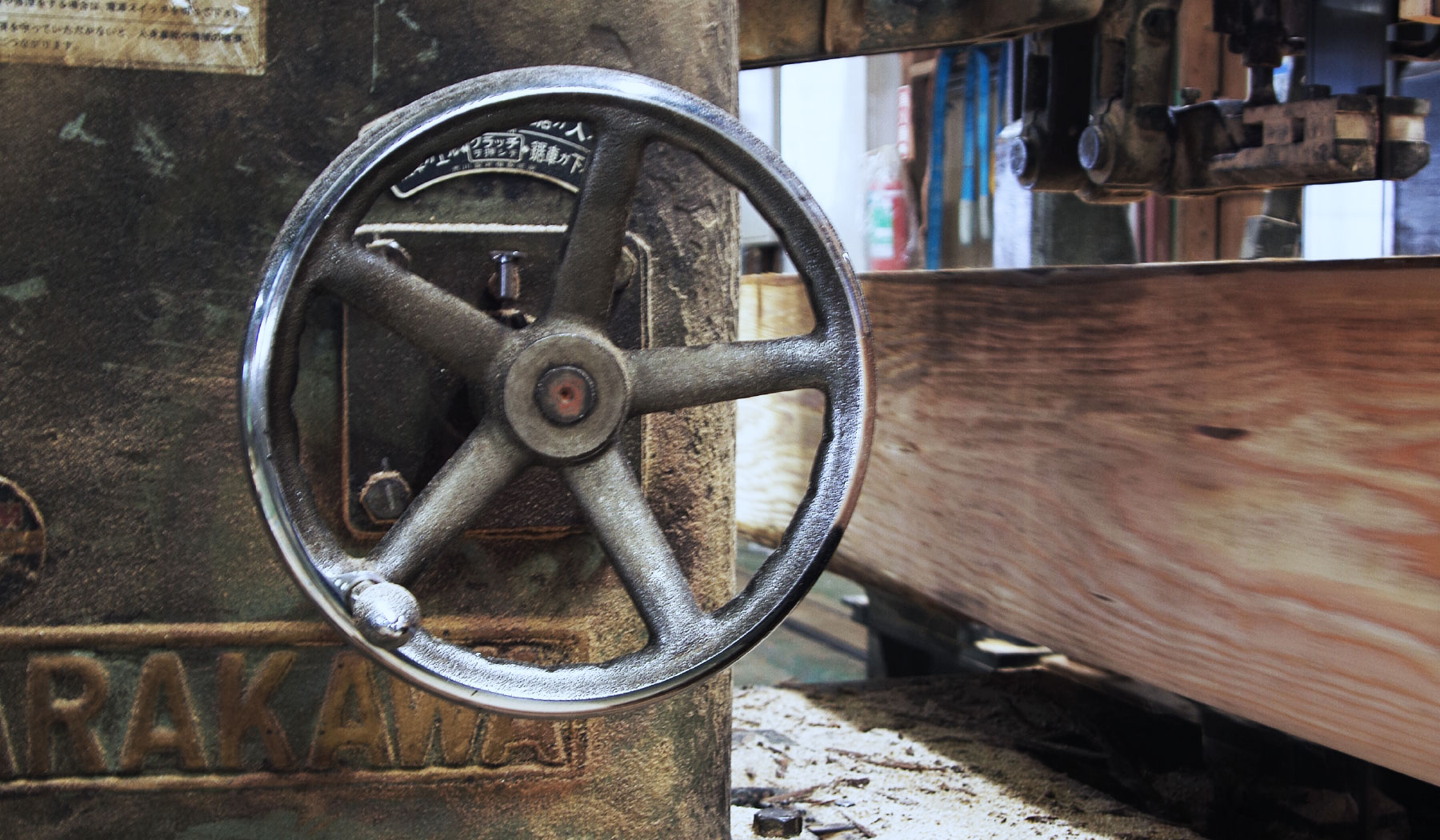
機械の話
機械は通すが常に人の手はかかる。
時代は代わり、精度の良い機械が当たり前となっても、
必ず職人の一手間は必要になる。
ほとんどの機械は昔から変わりません。ですが、新しい機械も導入され、安全に精度の良いものをまとめてつくれるようになりました。しかしそれは共通部品のような量産するものを速くつくることには適していますが、規格外の部材をつくるときは、アナログな機械を使います。機械はただ流す訳ではなく、木の方向や向きを決めて流さなければ割れたり、めくれたりします。㎜単位で削ることを意識しないと寸法はずれてしまいます。また、機械を使い続ければ、刃は切れなくなり、その刃を研げばまた仕上がり具合が変わります。常に変化する機械を職人は感覚で見ていきます。
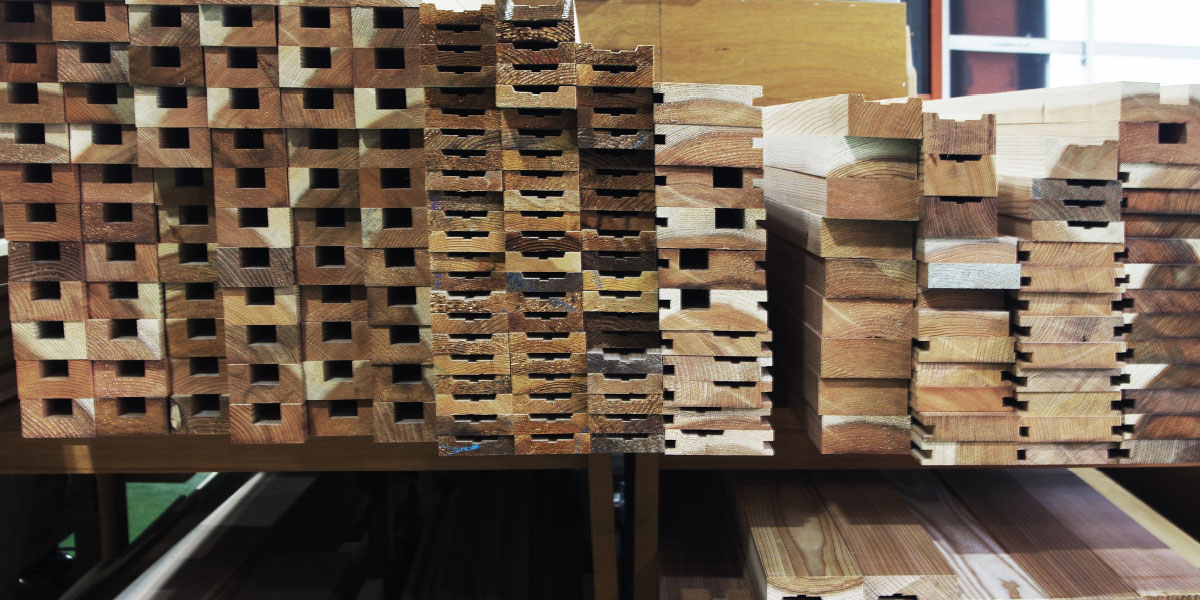
原木が部材にかわるまで
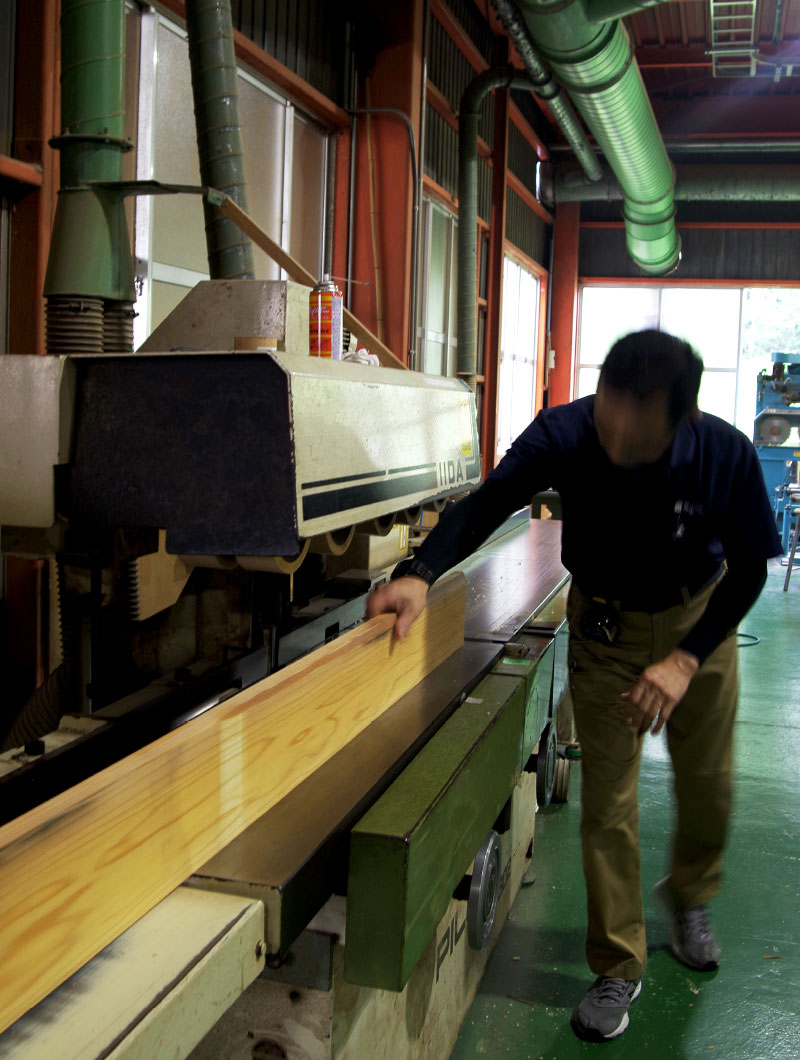
まず、製材機で原木を割ります。そこから板を乾燥させ、もう一度仕上がりに近いサイズに削っていき、更に別の機械で、削りしろを見ながら細かく削っていきます。
その後、直角を出す機械で木のねじれをとり、真っ直ぐにし、直角を出し、また別の機械で厚みと幅を決め、この時点で、真っ直ぐな四角の部材ができ、正寸に仕上げます。
ようやくここからがスタート。鴨居の溝をつけたり、家具や建具の部材へと加工していきます。最後にサンダーをかけ、塗装するための木地をつくります。
木材はほぼ下ごしらえが全てです。一つの部材をつくるために必要な時間と手間と職人の技術は既製品とは違う、特別なものを生み出す事が出来ます。
技術は受け継がれながらも
新しい技術を取り入れていく。
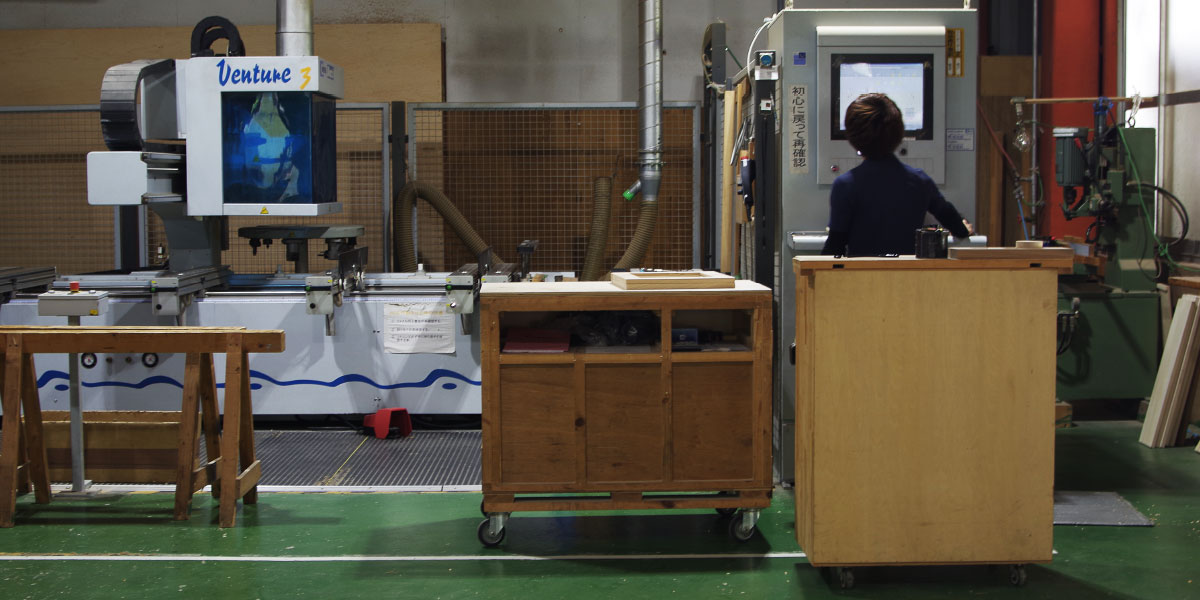
時代の変化と共に量産は必要となり、十数年前、木材加工の汎用機が導入されました。パソコンにデータを入れ、プログラムで刃物を選び、加工の指示をし、木材を切り、ドリルで穴を開け、削り、くり抜くことをします。この機械が導入される前はすべて手作業で加工していました。どうしても生じる仕上がりのムラはこの機械によって改善され、また、熟練の職人ではなくても、木材の加工は容易になりました。しかし、機械で仕上げたものはやはり荒く、必ず職人の一手間が必要になってきます。